Navigating Changing Healthcare Landscape and Needs
Healthcare constantly changes. From the ups and downs of routine care to the toll of extraordinary events, like the ongoing COVID-19 pandemic, hospitals and other medical providers aim to steer toward steady grounding. This, of course, means maintaining a strong workforce, ample inventory and a healthy bottom line to meet the rising tides and costs of care. COVID-19 propelled healthcare into a whole new level of unforeseeable challenges. The focus, for everyone, heightened on preventing the spread of the highly contagious and potentially deadly disease. Consequently, personal protective equipment (PPE), COVID-19 test kits and other must-have safety and clinical items, for example, have shifted to a premium at the front lines of care.
“PPE always has been a critical component of patient care, however the volume of PPE required has increased dramatically,” addresses Ashley G. Anderson Jr., MD, MS, CMO, Promega Corporation. “Patient encounters that would have required no PPE are now performed with full protective measures. This has resulted in shortage, the need to re-use items previously considered ‘single-use,’ hoarding, and a lack of effective allocation within many institutions. Personnel in high-risk settings may be re-using items, while inventory in other areas remains unused.”
Several state and local governments and communities rolled out new health and safety guidelines for the public. As a result, additional strain was placed on PPE demand and availability.
“Due to state-wide mask mandates, paranoia and shortages of commercial products, these items tend to make their way out of medical facilities and into the general population,” Dr. Anderson, Jr. continued. “Securing this vital inventory has become a necessity.”
Tracking and safeguarding PPE is a fundamental part of healthcare facility operations and safety. People’s lives ultimately depend on it, stresses Matt Tourdot, VP, Product Management, Terso Solutions.
“Too little inventory of critical items can have life or death consequences,” Tourdot explains. “Too much inventory leads to excess costs. This has only gotten more difficult due to the COVID-19 pandemic. Now, items that were relatively easy to manage, such as PPE, are incredibly challenging.”
Getting on Track with PPE, Testing and Medical Supply Management
Now is the time, urges Tourdot, for hospitals and healthcare facilities to streamline management of PPE and medical supplies and equipment to meet the needs of the current state of care and events yet to come.
Radio-frequency identification (RFID) technology can be used to identify and track inventory across various industries. The RAIN RFID-based automated inventory management systems by Terso Solutions have become the standard for supply chain applications in retail and in healthcare. These systems have been used in many hospitals, pharmacies and other settings, and help ensure that necessary resources are on hand when staff need them.
“Hospitals need to know that they have enough of all the items that are needed for all the possible procedures for the foreseeable future,” he said. “They are, at the same time, being asked to cut costs and reduce inventory levels. The only way to effectively do this is with an automated system that provides real-time visibility, item traceability, and security features that prevent loss. RAIN RFID systems fit perfectly.”
Some people may think that RFID systems are only for high-cost items such as medical devices, or priceless items such as donated human tissue. Those items are accommodated but, in a healthcare environment, especially today, critical items also can be low-cost items, like masks, shields, gloves, sutures, catheters and others. Every item used in a procedure, no matter its cost, is crucial.
RAIN RFID features include:
- COVID-19 test kits and samples taken using the test kits can be stored, tracked and secured in enclosures.
- Refrigerators and freezers add the benefit of remotely tracking the temperature and whereabouts of the COVID-19 test samples, which require temperature control, and therefore should be stored in a laboratory-grade refrigerator or freezer.
- Tags can be applied to just about anything – small items, big items, metal, liquids and more.
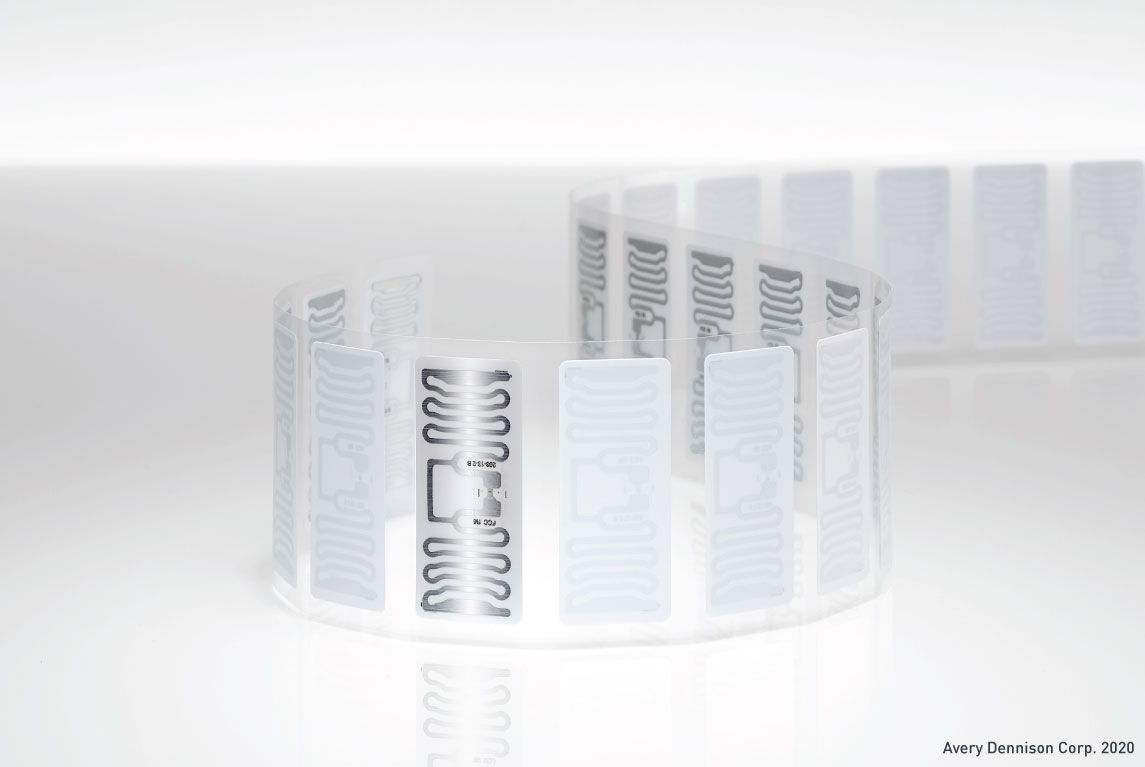
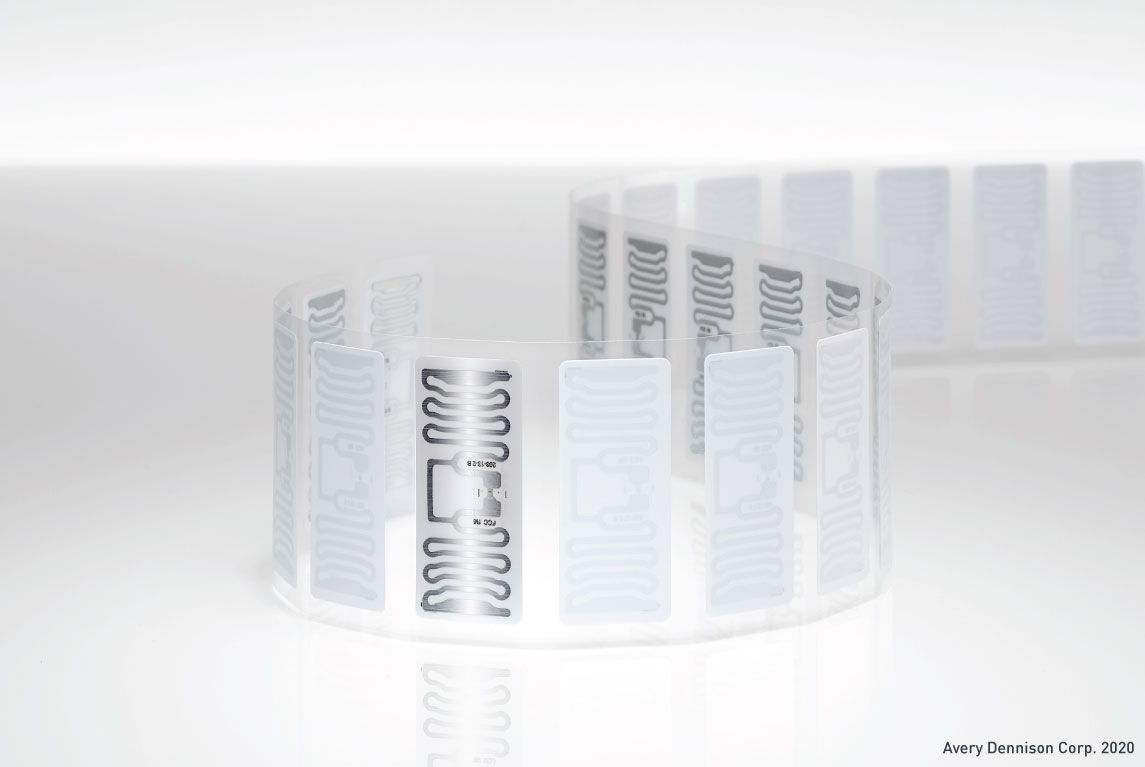
RAIN RFID systems allow healthcare providers visibility into what items are in stock, where those items are located, and transaction history indicating who took the items and when. All RFID technologies and protocols have unique benefits and applications where they are best suited. The benefits of ultra-high frequency (UHF), however, make it the clear choice for supply chain solutions, such as inventory management. The primary benefits of UHF are:
- Read distance – tags can be read at 10 to 30 feet and even more in some cases, compared to the other technologies where the read distance is from fractions of an inch up to a few inches. This is important for all supply chain applications where items are spread out in a warehouse, supply room or a freezer. This also enables the tags to be read with a variety of sensor types such as portals, handheld devices, freezers, and more.
- Speed – thousands of tags can be read automatically by a single sensor in just a few seconds with greater than 99.9% accuracy. This allows for products built with this technology to provide accurate real-time information.
- Adoption/Technological Advancement – wide-spread adoption of the systems has driven investments and advancements in innovation and cost reduction. It also means that there are countless different tag options available in different sizes and form factors.
The systems also can provide contextual information such as temperature, which is critical for biologics. Expired items can be removed from stock and items about to expire can be prioritized for use. Slow moving inventory can be moved to a different location with higher usage. Product recalls can be managed because the system will tell where every affected serial number product is located.
Obviously, with COVID-19, PPE is something that needs a high level of visibility and management. These systems can be used to prevent loss or pilfering. The enclosures provide security by requiring a user to present a valid pass/badge to unlock the doors. This allows inventory managers to limit access to only those who should have access. Passes can be managed through software, so new users can be added and access privileges can be set up per enclosure.
Optimizing Data and Reporting
The RAIN Alliance created the brand RAIN RFID to help companies and consumers easily identify RFID solutions that comply with the ISO/IEC 18000-63 and GS1 EPC Gen 2 standards. At its core, this standardized UHF wireless technology allows billions of everyday items to connect to the internet. Once connected, data regarding these items can be gathered and processed to provide intelligence and context regarding the items, which, in-turn, enables business processes that use this data to create value and efficiency.
The systems give tagged items a unique identity and the ability to communicate that identity wirelessly. Hardware and software then can be built to leverage this ability. Tags can be applied at the manufacturer, a distributor, the hospital/end-user site or any combination of these. The tagged items then need to be associated in the software. This means that the software needs to be told that the RFID tag that was applied represents, or is synonymous with, the item that it was applied to. Once tagged and associated, the items now can communicate with any category of RAIN RFID sensor.
Hospitals may choose any combination of sensors including secure medical cabinets, refrigerators, freezers, ultra-low temperature freezers, handheld scanners, ceiling-mounted sensors, desktop scanners, or loading dock portal sensors. The sensors can be placed anywhere that inventory is stored or used, from the loading dock to central stores to the point of use and anywhere in between.
The data captured from the tags and sensors is processed by the device, packaged into a usable format, and then sent to our cloud-based data platform. The platform organizes the data and makes it available to be consumed by the inventory management software. The software transforms the RFID data into user-friendly, visual information and provides the reports and tools that allow hospitals to optimize their inventory. There are all kinds of reporting possibilities including basic inventory on-hand reports, PAR-level reports, expiry reports, audit reports, temperature reports, and more. In most cases the reports that are available “out of the box” can also be supplemented with custom reporting tools.
Integration of the data from the automated inventory management system into other business systems used by the hospital is a huge part of the value that can be gained from adopting automation. A robust integration can eliminate any manual, human intervention in data sharing, minimize the possibility of errors, and make the data more likely to be used for the benefit of the organization.
Accessing Technical Service and Support
Many companies who offer automated inventory management systems require that customers use their packaged software. One of the important benefits of the Terso system architecture is that you can use whatever software you prefer. Terso uses an open Application Programming Interface (API) that allows integration into any software system. Partnerships include many trusted healthcare software providers whose software systems already have been integrated with the system.
Since all the inventory management devices and software systems are connected via the internet, the status of the systems can be remotely and continuously monitored from anywhere in the world. Technical support professionals are continuously monitoring system status and can provide information and system alerts to customers. Alerts also can be automated. Users can subscribe to the types of alerts that they are interested in and receive email or SMS alerts in real time. Some examples of the alerts include “freezer door left open,” “temperature outside of specified range,” or “internet communication lost.” Of course, customers can also always reach out to the technical support team directly via phone or email.
Planning for Future Healthcare and Events
In conclusion, now is the time for hospitals and healthcare facilities to streamline management of PPE and medical items needed to protect staff and provide the safest possible care for patients, ahead of another crisis.
“Healthcare entities must spend time and money on contingency planning and effective inventory management,” Dr. Anderson, Jr. emphasizes. “Virtually every population health scientist, every epidemiologist and every infectious disease specialist had acknowledged the likelihood of a pandemic prior to SARS CoV-2. It was never a question of ‘if,’ but rather ‘when.’ Despite this warning, little was done to prepare. Healthcare institutions and society must allocate space and create systems capable of managing personnel and supplies critical to fighting the next pandemic. We cannot afford to fight the next war as we are fighting this one.”